Мойка изделий методом струйной обработки в туннельной камере
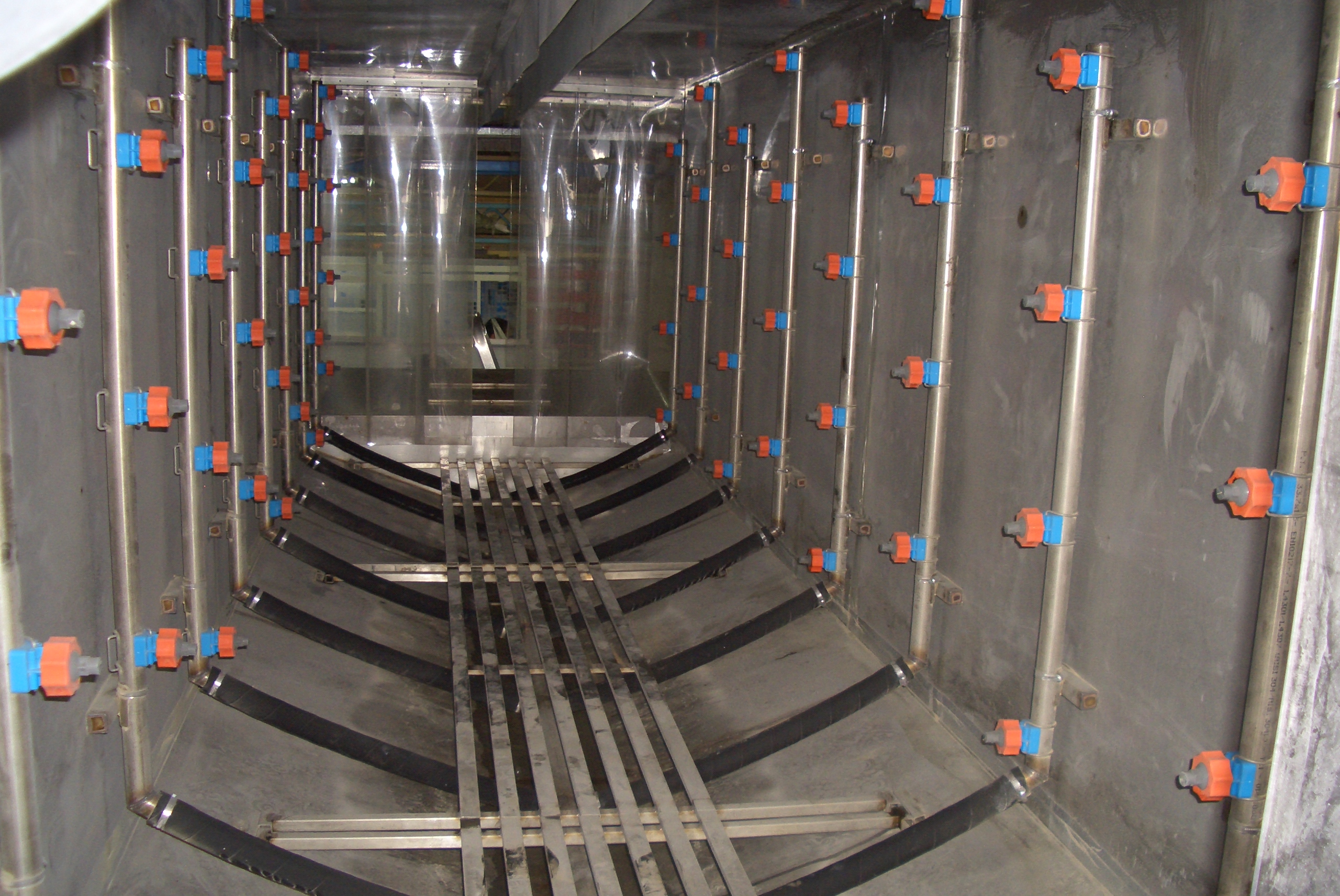
Достоинства подготовки поверхности методом струйной обработки в туннельной камере:
- максимальная производительность, возможность применения струйной обработки в составе единого конвейера и для подготовки, и для окраски изделий.
Метод струйной обработки в туннельной камере, в отличие от обычной камеры струйной обработки, является не цикличным, а непрерывно действующим.
Участок подготовки поверхностей методом непрерывной струйной обработки в туннельной камере обычно состоит из следующих компонентов:
- камера струйной обработки туннельного типа с зонами обработки, в которых смонтированы коллекторы с форсунками;
- конвейерная транспортная система непрерывного действия;
- ванны с моющими жидкостями;
- агрегат нагрева моющих жидкостей с автоматикой поддержания заданной температуры;
- насосы с запорно- регулирующей трубопроводной арматурой;
- система вытяжной вентиляции.
Туннельная камера разделена на зоны по количеству стадий обработки. В каждой зоне смонтированы коллекторы с форсунками для подачи моющих жидкостей под давлением на изделия. Коллекторы и форсунки расположены внутри камеры таким образом, что изделие, перемещающееся вдоль камеры, обрабатывается в каждой зоне струями из форсунок со всех сторон, охватываются все поверхности, подлежащие обработке.
Перемещение изделий в туннельной камере осуществляется непрерывно с помощью подвесного конвейера.
Под туннельной камерой расположены ванны с моющими жидкостями. Количество ванн (обычно до трех) соответствует количеству зон обработки. Количество ванн, состав моющих жидкостей и их температура определяется применяемой технологией подготовки. Каждая ванна имеет свой электронасос, подающий жидкость в коллектор с форсунками. Ванны могут быть оборудованы системой подогрева и автоматического поддержания заданной температуры рабочей жидкости. Ванна с подогревом моющей жидкости имеет стенки с теплоизоляцией, что позволяет уменьшить потери тепла. Каждая ванна имеет также насос с соответствующей запорно-регулирующей арматурой для наполнения и слива.
В процессе работы туннельной камеры все жидкости распыляются через форсунки в своей рабочей зоне и стекают обратно в соответствующие ванны. Проходя последовательно через каждую зону струйной обработки, изделие подвергается воздействию поочередно всех моющих жидкостей, предусмотренных техпроцессом. Длина каждой зоны в туннельной камере зависит от скорости конвейера и необходимой продолжительности обработки изделия каждой жидкостью.
Между зонами струйной обработки предусмотрены свободные от коллекторов и форсунок участки туннельной камеры, которые необходимы для стекания остатков моющей жидкости с поверхностей изделий. Таким образом, наличие этих свободных участков позволяет минимизировать перенос моющих жидкостей из одной ванны в другую. Длина свободных участков зависит от скорости движения конвейера, от площади и расположения поверхностей изделий.
Туннельная камера имеет систему вытяжной вентиляции, которая в процессе работы удаляет пары моющих жидкостей из камеры за пределы производственного помещения.
Вернуться на основную страницу оборудования подготовки поверхности